Manufacturer Certifications vs. State Licenses: Managing Both Simultaneously
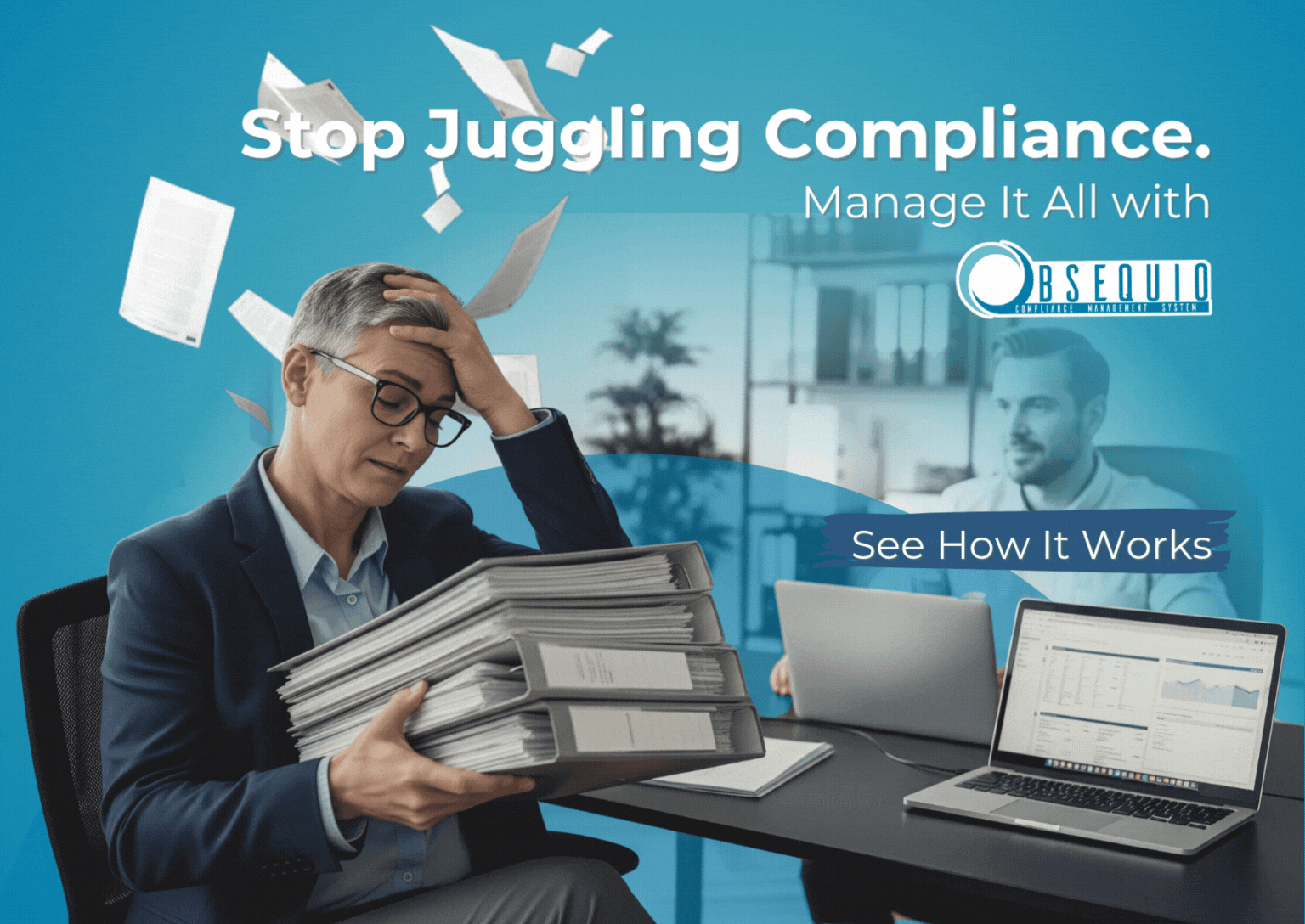
Your best technician just called with news that makes your stomach drop. The customer is asking for proof of his Axis certification for tomorrow's installation, but nobody can find the current certificate. His state license? Perfect. His manufacturer credentials? Missing in action.
Welcome to the dual compliance nightmare that's costing security companies projects, credibility, and sleep.
The Hidden Complexity of Security Industry Compliance
Security professionals operate under a compliance framework that would make accountants weep. You're not just managing one set of requirements - you're juggling multiple, overlapping compliance obligations that operate on different schedules, have different renewal processes, and require different documentation.
State Licensing Requirements Across 44 states and the District of Columbia, security professionals need valid licenses to legally install, maintain, sell, support, or monitor security systems. These licenses typically require:
- Initial applications with background checks
- Examination passage
- Continuing education credits
- Annual or biennial renewals
- Fee payments ranging from modest to substantial
Manufacturer Certification Requirements But legal authorization is only half the battle. Equipment manufacturers require separate certifications that demonstrate technical competency with their specific products. These certifications involve:
- Product-specific training completion
- Technical examinations
- Hands-on installation demonstrations
- Renewal cycles ranging from one to three years
- Varying continuing education requirements
The challenge? These two compliance worlds rarely communicate with each other.
Where Dual Compliance Goes Wrong
The Certification Time Bomb Your technician's state license shows two years remaining. His manufacturer certifications? Three different expiration dates across six different vendor programs. When Honeywell requires renewal in March, Bosch in July, and Axis in October, tracking becomes a full-time job.
Most security companies discover certification gaps at the worst possible moments - during bid processes, customer audits, or when manufacturer representatives ask for proof of current credentials.
The Documentation Disaster State licenses typically generate official certificates with clear expiration dates. Manufacturer certifications might exist as portal logins, PDF certificates, digital badges, or simple email confirmations. Some vendors update their tracking systems regularly. Others haven't refreshed their databases in months.
When audit time arrives, reconstruction becomes a detective game. Which portal has the current information? Was that certification completed before or after the manufacturer changed their requirements? Did the online training include the hands-on component?
The Continuing Education Conflict Many states accept manufacturer training for continuing education credits. But tracking which training satisfies which requirements across multiple jurisdictions and vendor programs requires mathematical precision that spreadsheets can't provide.
Your technician completes 16 hours of Genetec training. Does that satisfy his Virginia continuing education requirement? What about his Maryland license? Did he complete the courses before or after his renewal date? Does Genetec training count toward his Access Control specialty certification?
The Cost of Compliance Confusion
Lost Project Opportunities Major commercial projects increasingly require proof of current certifications before contract award. When customers request documentation for specific manufacturer credentials, delays in providing proof can eliminate you from consideration.
Healthcare facilities, government installations, and enterprise customers often maintain approved vendor lists based on current certifications. Missing or expired credentials remove you from future opportunities before you know they exist.
Customer Relationship Damage Nothing destroys professional credibility faster than discovering compliance gaps during active projects. When your lead technician can't prove current certification for the equipment he's installing, customers question your entire operation's competency.
Operational Inefficiency Technicians spend billable hours researching their own compliance status instead of generating revenue. Administrative staff waste time cross-referencing multiple systems, chasing down expired credentials, and reconstructing certification histories.
Regulatory Risk Exposure State licensing boards don't care about manufacturer certification status when they investigate compliance violations. Manufacturer audits don't consider state licensing when they evaluate partner qualifications. Each compliance failure creates separate liability exposure.
The Unified Tracking Solution
Smart security companies are abandoning the multi-system approach in favor of unified compliance management platforms that monitor both state licenses and manufacturer certifications simultaneously.
Centralized Visibility Instead of checking state licensing boards, manufacturer portals, and training databases separately, unified systems provide complete compliance pictures for each technician. One dashboard shows state license status, manufacturer certification expiration dates, continuing education credits, and upcoming renewal requirements.
Automated Coordination Advanced systems recognize relationships between different compliance requirements. When a technician completes manufacturer training that satisfies continuing education requirements, the system automatically updates both records. When state license renewal approaches, the system identifies relevant manufacturer training that could satisfy CEU requirements.
Proactive Management Rather than discovering expired certifications during project bids, unified systems provide advance warning of upcoming expirations across all compliance categories. Automated reminders coordinate renewal timing to maximize efficiency and minimize administrative burden.
The Strategic Implementation Approach
Assessment Phase Begin by cataloging all compliance requirements your company currently manages. State licenses, manufacturer certifications, continuing education obligations, and specialty credentials each require different tracking approaches. Document current renewal cycles, fee structures, and documentation requirements.
Consolidation Planning Identify opportunities to coordinate renewal activities. Can technician training be scheduled to satisfy both manufacturer requirements and continuing education obligations? Can certification renewals be clustered to reduce administrative overhead?
Documentation Standardization Establish consistent documentation procedures for all compliance activities. Whether dealing with state licensing boards or manufacturer certification programs, standardized record-keeping prevents information gaps and simplifies audit processes.
Monitoring Integration Implement systems that track both compliance categories simultaneously rather than managing them separately. Integration prevents conflicts between different requirements and identifies opportunities for efficiency improvements.
The Competitive Advantage
Security companies that master dual compliance management gain significant competitive advantages. They bid confidently on projects knowing their team's qualifications are current and documented. They avoid project delays caused by certification discoveries. They maintain customer relationships built on demonstrated competency rather than hoped-for compliance.
Most importantly, they operate efficiently. Instead of reactive compliance management that responds to problems, they maintain proactive oversight that prevents issues before they impact operations.
The Technology Enable
Modern compliance management platforms designed specifically for the security industry understand the dual nature of compliance requirements. They track over 500 different compliance data points covering both state licensing requirements and manufacturer certification programs.
These systems don't just remind you when renewals approach - they coordinate renewal activities to maximize efficiency and minimize disruption. They maintain documentation that satisfies both regulatory audits and manufacturer partner requirements.
Integration Capabilities Advanced platforms integrate with manufacturer training systems, automatically updating certification status when courses are completed. They coordinate with continuing education providers to ensure credits are properly allocated across different requirements.
Reporting Functions Comprehensive reporting capabilities provide a compliance status overview across entire teams, identify upcoming requirements by technician or location, and generate documentation for customer audits or regulatory inspections.
The Implementation Reality
Transitioning from fragmented compliance tracking to unified management requires initial investment in system setup and data migration. However, the alternative - continuing to manage multiple compliance requirements across separate systems - guarantees continued inefficiency and risk exposure.
The security industry's regulatory complexity isn't decreasing. Manufacturer certification requirements are becoming more stringent. State licensing boards are increasing oversight. Customer compliance expectations continue growing.
Companies that solve dual compliance management now position themselves for sustained competitive advantage. Those who continue to manage compliance reactively across multiple systems face increasing operational friction and risk exposure.
Ready to unify your compliance management approach? Stop juggling state licenses and manufacturer certifications across separate systems. Implement unified tracking that monitors both simultaneously, coordinates renewal activities efficiently, and provides complete compliance visibility for your entire team. Your operations will run smoother, your bid processes will be more confident, and your customer relationships will strengthen through demonstrated competency.